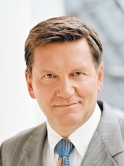
By Bjorn Fehrm
January 19, 2024, ©. Leeham News: We are discussing the different phases of a new airliner program. After covering the Design and Production, we now look at the Operational phase of a new airliner family.
For the operational phase, the airplane must pass scrutiny for Continued Airworthiness. Today, we discuss the biggest item in a regulator’s Instructions for Continued Airworthiness: the required Maintenance to keep an airliner airworthy.
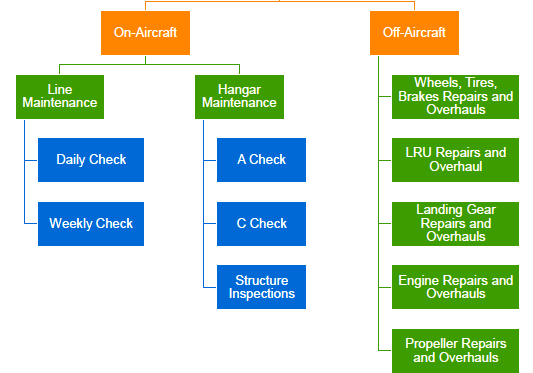
Figure 1. A typical maintenance program for an airliner. Source: ATR.
Airliner Maintenance
For an aircraft to keep its operational certification, it must be subject to a maintenance program approved by the local regulator. A country regulator, in turn, relies on a proposed maintenance program from the OEM, which was developed in a prescribed procedure called MSG-3 (from Maintenance Steering Group’s 3rd process version).
In addition to the OEM’s proposal for a maintenance program, the local regulator can prescribe extra conditions and actions to cater to local weather conditions or operational stresses (like a dusty environment). In the end, it’s the local regulator that decides what must be in an aircraft’s maintenance program that the operator presents to him for approval.
Figure 1 describes the main blocks in a modern maintenance program as suggested by an OEM. The chart is from an ATR maintenance brochure from 2020, which has a good high-level description of the maintenance program for the aircraft.
But before we go into a modern maintenance program, let’s look at the history of airliner maintenance. It went from a non-regulated and individual process for each airliner to a structured US regulator (the FAA)-demanded maintenance program as the big jet airliners (Boeing 707, Douglas DC-8) were introduced. The focus on a safe flight of passengers resulted in the first version of a Hard-Timed maintenance process.
Components in an aircraft were set a use limit, after which it should be removed (for instance, a hydraulic pump), sent to a repair shop, and “Zero-timed” by exchanging worn components. The maintenance levels and times were grouped into groups denoted by letters. We now give an example of a typical early Hard Timed system. It uses Flight Hours (FH) as the limit, but real systems used a combination of Flight Hours, Flight Cycles (FC), and Calender time limits:
- Line daily check: A mechanic checks during the night or in the morning before the aircraft goes on the first mission. Examples of checks include visual inspection around the aircraft, oil levels in engines and gearboxes, checks of tires and brakes, landing gear legs for leaks, filter conditions, oxygen and fire extinguisher fill levels, etc.
- Line weekly check: A thorough visual check of all moving parts, safety equipment are run through test programs, cabin items such as chairs, safety belts, oxygen systems are checked and tested, etc.
- The hangar A-check: Repeated after every 500 Flight Hours (FH). Visual inspections of areas beneath covers and hatches, in landing gear bays, cargo area, fuselage keel area. Lubrication of service points on doors, flaps, slats, movables, and landing gear. Checks on hydraulic, bleed, sewage, water, and electric systems. APU runs and performance tests.
- The hangar B check: More extensive hangar checks at every second A check timeout, i.e. 1000 FH, 3,000FH, 5,000FH…
- The hangar C-check: done every second B check timeout, i.e., 2,000FH, 4,000FH… The program from the A and B checks are now complemented by deeper checks on the systems in the aircraft, and the propulsion powerplants are run to check condition and performance.
- The heavy hangar D-Check: Every 12,000FH or 10 to 12 years of service. This is the expensive and time-consuming check where much of the interior and some of the aircraft structure is removed to gain access to corrosion and fatigue inspections of the whole aircraft. Systems are removed, inspected, and, if needed, overhauled, as are engines and APUs. Structures and parts with wear are repaired or replaced. Often, the aircraft paint is stripped, and the aircraft gains a new livery.
The above hard-timed program did maintenance on a number of parts irrespective of how the aircraft was used. There is a major difference in wear on the aircraft if the climate is benign or harsh, like sandy or dusty. And many short hops are tougher on the aircraft than longer sectors. The hard time process also did not allow for systems where system self-checks can determine the time for overhaul, so-called On-Condition Maintenance.
Gradually, the airframe OEMs, the regulators, and the maintenance industry worked to change the hard-time maintenance systems to a more flexible and On Condition-based system. This is the system we have today, called MSG-3. We go through what it means in the next Corner.
Related